How our design boosted production analysis and brought in new revenue
Honeywell Forge P+
How our design boosted the production process and brought in new revenue
Honeywell Forge P+
How our design boosted the production process and brought in new revenue
Honeywell Forge P+
How our design boosted the production process and brought in new revenue
Honeywell Forge P+







ROLE
ROLE
Led a team of 3, UX Research and Design,
Conceptual testing
Led a team of 3, UX Research and Design,
Conceptual testing
Led a team of 3, UX Research and Design, Conceptual testing
IMPACT
IMPACT
Eliminating up to 45% of avoidable corrective maintenance costs
Boosting OEE to save up to 25% of equipment value, improving asset availability by up to 15% and performance by up to 10%.
Eliminating up to 45% of avoidable corrective maintenance costs
Boosting OEE to save up to 25% of equipment value, improving asset availability by up to 15% and performance by up to 10%.
Eliminating up to 45% of avoidable corrective maintenance costs
Boosting OEE to save up to 25% of equipment value, improving asset availability by up to 15% and performance by up to 10%.
What is the problem?
Empowering P+ users to analyze production losses in their plants to do effective RCA and take action.
Empowering P+ users to analyze production losses in their plants to do effective RCA and take action.
Our goals were to
Maximize productivity and figure out opportunities to make improvements.
Maximize productivity and figure out opportunities to make improvements.
Standardize buckets of losses - Loss event concerning product, and equipment.
Standardize buckets of losses - Loss event concerning product, and equipment.
Identify the bad actors and target the most important ones and create projects to create fixes.
Identify the bad actors and target the most important ones and create projects to create fixes.
Also, I was awarded a BRONZE Bravo award for successfully translating the stakeholder inputs.
Also, I was awarded a BRONZE Bravo award for successfully translating the stakeholder inputs.





Also, some cool data Viz were explored
See Solution
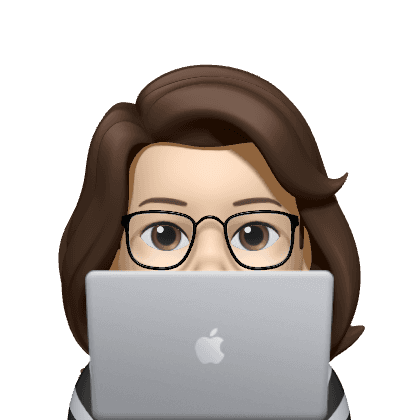







Such a complex problem, what was our
plan here?
DEFINING USECASES
We spoke to the SME's from the different industries that were Involved to
identify the JTBD!
Such a complex problem, what was our plan here?
DEFINING USECASES
We spoke to the SME's from the different industries that were Involved to identify the JTBD!
DEFINING USECASES
Such a complex problem, what was our plan here?
We spoke to the SME's from the different industries that were Involved to identify the JTBD!




Such a complex problem, what was
our plan here?
DEFINING USECASES
We spoke to the SME's from the different industries that were Involved to identify the JTBD!




How did we
amplify the function
of the design
How did we amplify the function of the design?
How did we amplify the function of the design?
We ran a UX research kick-off workshop with the team to understand the key personas for the MVO release and we started putting together a couple of research scripts to get detailed insights into their world.
We wanted to make sure that the challenges and solutions that are developed are applicable industry-wide and not just for one specific use case.
We ran a UX research kick-off workshop with the team to understand the key personas for the MVO release and we started putting together a couple of research scripts to get detailed insights into their world.
We wanted to make sure that the challenges and solutions that are developed are applicable industry-wide and not just for one specific use case.
01
Plant Manager
"I need to run safely, maximize production, keep assets running without disruption and minimize energy consumption."
02
Process Supervisor
We conducted user interviews, surveys, and analyzed in-app analytics to understand the pain points and user needs. We also studied competitor apps and industry trends to gather insights
03
Area/Unit Manager
We conducted user interviews, surveys, and analyzed in-app analytics to understand the pain points and user needs. We also studied competitor apps and industry trends to gather insights
04
Maintenance Manager
We conducted user interviews, surveys, and analyzed in-app analytics to understand the pain points and user needs. We also studied competitor apps and industry trends to gather insights

01
Plant Manager
"I need to run safely, maximize production, keep assets running without disruption and minimize energy consumption."
02
Process Supervisor
We conducted user interviews, surveys, and analyzed in-app analytics to understand the pain points and user needs. We also studied competitor apps and industry trends to gather insights
03
Area/Unit Manager
We conducted user interviews, surveys, and analyzed in-app analytics to understand the pain points and user needs. We also studied competitor apps and industry trends to gather insights
04
Maintenance Manager
We conducted user interviews, surveys, and analyzed in-app analytics to understand the pain points and user needs. We also studied competitor apps and industry trends to gather insights

01
Plant Manager
"I need to run safely, maximize production, keep assets running without disruption and minimize energy consumption."
02
Process Supervisor
We conducted user interviews, surveys, and analyzed in-app analytics to understand the pain points and user needs. We also studied competitor apps and industry trends to gather insights
03
Area/Unit Manager
We conducted user interviews, surveys, and analyzed in-app analytics to understand the pain points and user needs. We also studied competitor apps and industry trends to gather insights
04
Maintenance Manager
We conducted user interviews, surveys, and analyzed in-app analytics to understand the pain points and user needs. We also studied competitor apps and industry trends to gather insights

And then the key design opportunities
started to arise
And then the key design opportunities started to arise
And then the key design opportunities
started to arise
From our research, we prioritized these three core challenges for the MVO.
From our research, we prioritized these three core challenges for the MVO.

Lack of Loss
Monetization
Lack of Loss
Monetization
To understand how much the unit is making for them in terms of $, loss in DT hours.
To understand how much the unit is making for them in terms of $, loss in DT hours.

Loss
categorization
Loss
categorization
Lack of standard Loss Categorization system and easily accessible Equipment Parent Child Hierarchy (from CMMS system) so that loss events can be properly aggregated over different time periods and across different sites.
Lack of standard Loss Categorization system and easily accessible Equipment Parent Child Hierarchy (from CMMS system) so that loss events can be properly aggregated over different time periods and across different sites.
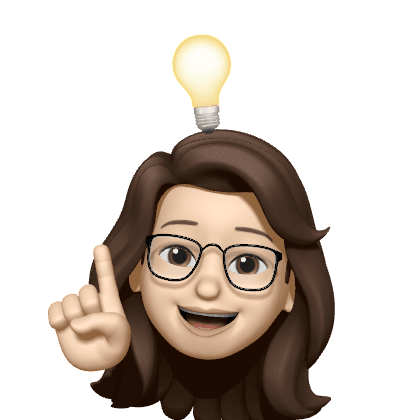
Actionable
Insights
Actionable
Insights
Existing solutions do not provide real time actionable insights for production loss improvement and efficiency. It needs to provide data that can be used to optimize operations.
Existing solutions do not provide real time actionable insights for production loss improvement and efficiency. It needs to provide data that can be used to optimize operations.
Defining the problem statements
Defining the problem statements
Defining the problem statements
Improve operations and production outcomes by identifying production bottlenecks and
inefficiencies and recommending actionable insights.
Improve operations and production outcomes by identifying production bottlenecks and inefficiencies and recommending actionable insights.
Improve operations and production outcomes by identifying production bottlenecks and inefficiencies and recommending actionable insights.
Streamline production tracking and analysis to identify root causes, track OEE events, and uncover patterns for continuous operational improvement.
Streamline production tracking and analysis to identify root causes, track OEE events, and uncover patterns for continuous operational improvement.
Maximize operations performance across the production unit/shop floor by understanding process bottlenecks ** by making performance metrics available in real-time.
Maximize operations performance across the production unit/shop floor by understanding process bottlenecks.
Determine the top opportunities for productivity improvements by gaining real-time visibility into uptime, downtime, production quality, asset availability, production output
Determine the top opportunities for productivity improvements by gaining real-time visibility into OEE and production metrics.
SO many ideas but we ideated with TPO and Func
Arch for the "best" solution
SO many ideas but we ideated with TPO and Func Arch for the "best" solution
SO many ideas but we ideated with TPO and Func
Arch for the "best" solution
SO many ideas but we ideated with TPO and Func Arch for the "best" solution
We conducted a design workshop with the cross-functional team to map out the features for the user stories.
We conducted a design workshop with the cross-functional team to map out the features for the user stories.
















Now to the fun part of
the project
Now to the fun part of the project
Now to the fun part of the project
Just a sneak peek! The UI is modified to maintain the NDA
Just a sneak peek! The UI is modified to maintain the NDA
Overview of Production and OEE metrics
Overview of Production and OEE metrics
Overview of Production and OEE metrics

Lack of Loss Monetization
Lack of Loss Monetization
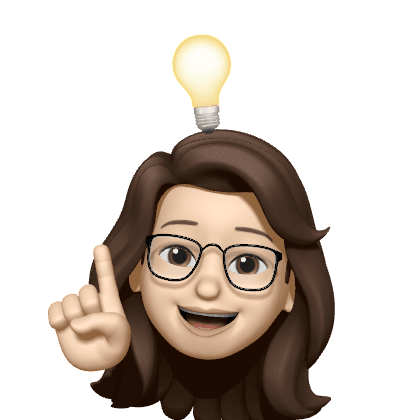
Automating Manual Processes
Automating Manual Processes
OEE overview: At the unit level, points the bad actors that are causing them to lose money and investigate the events causing it further.
Production overview: Helps to understand where am I gonna spend
my money to do capital projects to improve the the performance of
a unit or de-bottlenecking unit?
Evaluate key performance indicators: How much have the lost in terms of DT, $ and LBs is important to decide the source of these inefficiencies and whether is it worth investigating.
Address common issues: Examine recurring problems found by OEE and YIELD analysis and come up with solutions.
OEE overview: At the unit level, points the bad actors that are causing them to lose money and investigate the events causing it further.
Production overview: Helps to understand where am I gonna spend
my money to do capital projects to improve the the performance of
a unit or de-bottlenecking unit?
Evaluate key performance indicators: How much have the lost in terms of DT, $ and LBs is important to decide the source of these inefficiencies and whether is it worth investigating.
Address common issues: Examine recurring problems found by OEE and YIELD analysis and come up with solutions.







Measuring OEE to identify bottlenecks
Measuring OEE to identify bottlenecks
Measuring OEE to identify bottlenecks
Measuring OEE to identify
bottlenecks

Loss categorization
Loss categorization
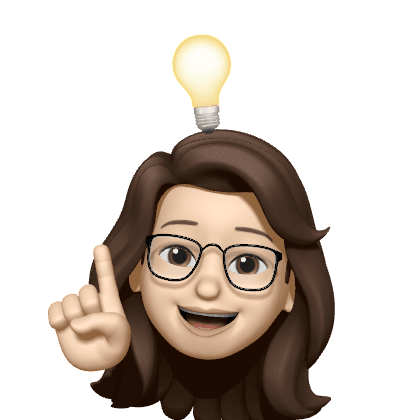
Actionable insights
Actionable insights
Start with OEE analysis: At the equipment level, OEE analysis aids in identifying the root causes of losses and inefficiencies.
Identify bottlenecks: To locate bottlenecks where equipment performance isn't at its best, use OEE data. This assists in setting priorities for improvement projects and focusing on particular equipment or workflows that have the biggest effects on overall performance.
Evaluate TEEP for the entire line: Taking into consideration both scheduled and unscheduled downtime, TEEP offers a more comprehensive view of the line's overall performance.
Production loss analytics: Ability to create pareto charts, pie charts, and bad actor lists based on equipment Tech ID, and various categories and subcategories.
Start with OEE analysis: At the equipment level, OEE analysis aids in identifying the root causes of losses and inefficiencies.
Identify bottlenecks: To locate bottlenecks where equipment performance isn't at its best, use OEE data. This assists in setting priorities for improvement projects and focusing on particular equipment or workflows that have the biggest effects on overall performance.
Evaluate TEEP for the entire line: Taking into consideration both scheduled and unscheduled downtime, TEEP offers a more comprehensive view of the line's overall performance.
Production loss analytics: Ability to create pareto charts, pie charts, and bad actor lists based on equipment Tech ID, and various categories and subcategories.






Also, some cool data Viz were explored
See Solution
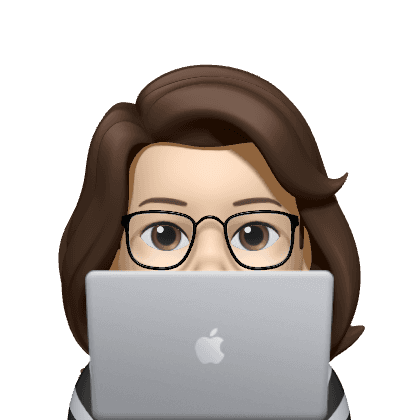
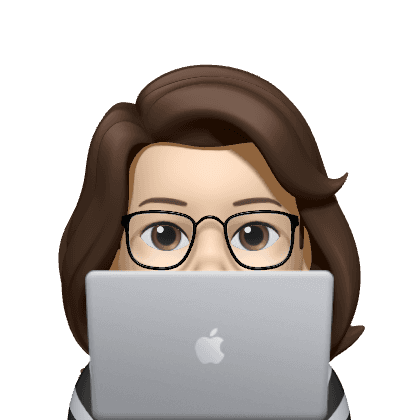








Also, some cool data Viz were explored
See Solution
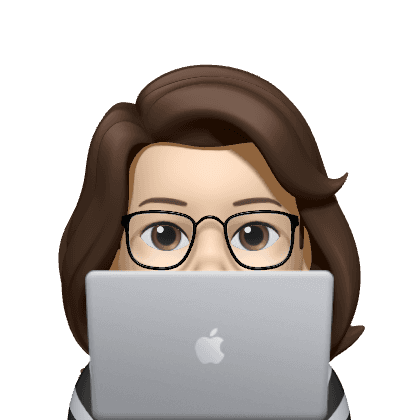







Measuring and validating
designs
Measuring and Validating designs
Measuring and Validating designs
To validate our design decisions we started with static concept prototypes. These helped us explore multiple ideas quickly that we could then narrow down further to start developing.
Every iteration we had some confidence in would then be shipped to the internal SMEs for us to use during meetings.
Once we gathered feedback from these groups we’d ship to a smaller % of internal SME to then gather feedback via user interviews.
We then continued to measure success through experimentation and various metrics like feature adoption, time spent, and data gathered from user interviews.
To validate our design decisions we started with static concept prototypes. These helped us explore multiple ideas quickly that we could then narrow down further to start developing.
Every iteration we had some confidence in would then be shipped to the internal SMEs for us to use during meetings.
Once we gathered feedback from these groups we’d ship to a smaller % of internal SME to then gather feedback via user interviews.
We then continued to measure success through experimentation and various metrics like feature adoption, time spent, and data gathered from user interviews.
25%
25%
25%
25%
Increase In User Retention
Increase In User Retention
8k
Daily Users
45%
45%
45%
reduction in maintenance costs
What did this project
teach me?
What did this project teach me?
What did this project teach me?
Product Strategy
A holistic product strategy is more important than the design feature itself.
Cross-Collaboration
Involving functional architect and technical product owners help to learn the know-how of the technicalities.
Leading a team
It was challenging to lead a team of 3 designers and handling the product management expectations at the same time, but this project taught me the soft skills to multi task and putting together an efficient plan.
Product Strategy
A holistic product strategy is more important than the design feature itself.
Cross-Collaboration
Involving functional architect and technical product owners help to learn the know-how of the technicalities.
Leading a team
It was challenging to lead a team of 3 designers and handling the product management expectations at the same time, but this project taught me the soft skills to multi task and putting together an efficient plan.
Don't stop, keep looking!
Don't stop, keep looking!