About Honeywell Forge P+?
P+ is a horizontal SaaS product that enables intelligent operations by combining asset performance, workforce insights and process analytics for distribution centers and industrial plants to increase productivity, speed of execution for greater efficiency.
See Solution
A quick 1-min overview
Why was it done?
P+ users are interested in learning about their site-level OEE and performing unit-level production analysis.
Managers are constantly trying to figure out what the production loss is for their plant, they do this to pinpoint where this production loss is coming from and then open up projects to fix these losses..
Our goals were to:
Maximize productivity and figuring out opportunities are to make improvements.
Standardize buckets of losses - Loss event with respect to product, and equipment.
Identify the bad actors and target the most important ones and create projects to create fixes.
Such a complex problem, so how did we break this down?
We spoke to the SME's from the industries that were Involved
Chemical
Oil & gas
Minning
Identifying the Personas and JBTD!
We ran a UX research kick-off workshop with the team to understand the key personas for the MVO release and we started putting together a couple of research scripts to get detailed insights into their world.
We wanted to make sure that the challenges and solutions that are developed are applicable industry-wide and not just for one specific use case.
Internal SME UX
research discussions
UserTesting
generative research
Business
Objectives
Production Impact Challenges
From our research, we prioritized these three core challenges for the MVO.

Lack of Loss
Monetization
Utilizing variable contribution margin = VCM for each prodcut

Loss
categorization
Lack of standard Loss Categorization system and easily accessible Equipment Parent Child Hierarchy (from CMMS system) so that loss events can be properly aggregated over different time periods and across different sites.
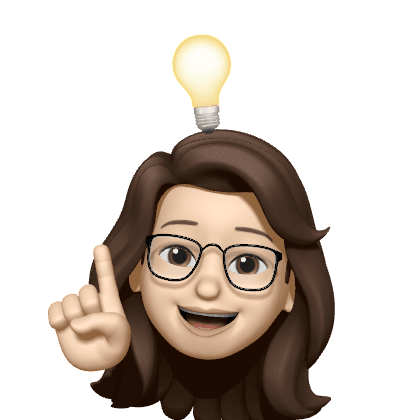
Actionable
Insights
Existing solutions do not provide real time actionable insights for production loss improvement and efficiency. It needs to provide data that can be used to optimize operations.
Design Thinking Workshop
We partnered up with Product managers and Technical product owners to come up with production impact analysis solutions that can reduce downtime and suggest effective action items.
Defining Experience Outcomes
We were able to map out the experience outcomes to drive the design solutions and make sure we were addressing the main
pain points.
User Flow Mapping
Since the product has so many modules and flows that needed to be interlinked, we laid out the user flow with the functional architect.
Just a sneak peek!
OEE The first step to measure product impact is to analyze the Overall Equipment Effectiveness of the units and monitor the volume generated to identify bad actors. Once identified, the plant manager does the root cause analysis to solve the problem.
Unit Level The step process is to get an understanding what is causing the reduction in OEE, by analyzing the contextual line timelines to
recognize patterns and highlights opportunities to improve the operations.
Learnings
The next step is concept testing with internal and external SMEs, validating with the horizontal PMs and clients. There were some insightful learnings though.
A holistic product strategy is more important than the design feature itself
Involving functional architect and technical product owners help to learn the know-how of the technicalities